Don’t get hit by a wave1….Don’t get too wet…and…Make sure you dry…
The best way to design for floods is to build in places where you don’t get floods. Yeah, right. We have gotten pretty good at predicting flood risk. The Federal Emergency Management Agency (FEMA) has identified Special Flood Hazard Areas (SFHA). We just don’t pay much attention and build there anyway. So if I can’t convince you to not build there I will try to help you reduce your risk. The new buzz word for this is “resiliency”. And yes, we were here before…more than once…(BSD-111: Flood and Hurricane Resistant Buildings, October 2006 and BSI-101: Rebuilding Houston, November 2017).
A bit of background - there are three common types of flood events:
- Fluvial (“river”) floods
- Pluvial (“flash floods and surface water”) floods
- Coastal (“storm surge”) floods
For all of them the basis of flood resistance or “resilience” includes the following:
- Elevate structures
- Protect service equipment
- Ensure that flood waters enter and exit the house
- Design and construct building assemblies that are able to get wet during a flood event, readily cleaned and subsequently dried
First, the obvious. All flood risk is reduced where the building floors are located above the base flood elevation (BFE) and where the slope of the land directs water away from the building. Raised slab and elevated pier foundations tend to be more robust and lower risk than slab foundations and crawl space foundations. Let me repeat….with all foundation approaches floors should be constructed above the base flood elevation (BFE) with the grade sloping away from the building (Figure 1a, Figure 1b and Figure 1c). Build as high as you can…the higher the better. In coastal areas the first level should be used for parking and storage (Photograph 1 and Photograph 2).
Figure 1a, Figure 1b and Figure 1c: All flood risk is reduced where the slope of the land directs water away from the building and where the building floors are located above the base flood elevation (BFE). Raised slab and elevated pier foundations tend to be more robust and lower risk than slab foundations and crawl space foundations.
Photograph 1: Build as high as you can…the higher the better.
Photograph 2: In coastal areas the first level should be used for parking and storage.
Raise heating, ventilation and cooling (HVAC) equipment above the BFE to prevent damage (Photograph 3). Raise electrical components – at least 12 inches above the BFE (switches, sockets, circuit breakers and wiring) – in order to reduce damage to the electrical system and the chance of fire from short circuits.
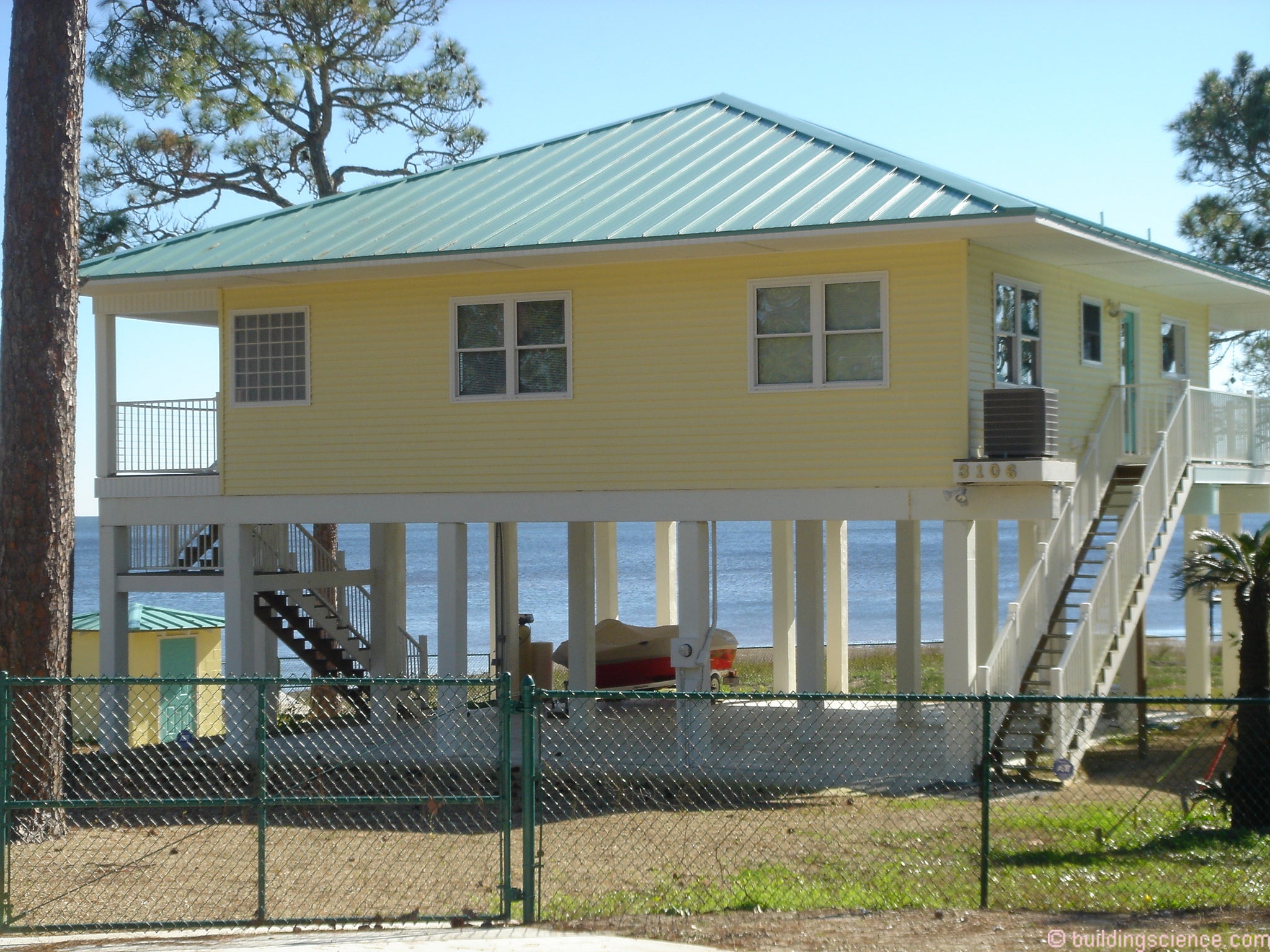
Figure 2 illustrates the use of concrete masonry block (CMU) to create a “raised slab foundation”. The first floor assembly is also masonry internally insulated with non-water sensitive rigid insulation. The second floor is wood framed. The roof construction is a vented attic.
Figure 2: Concrete Masonry Unit (CMU) Assembly - The first floor assembly is masonry internally insulated with non-water sensitive rigid insulation. The second floor is wood framed with continuous exterior rigid insulation and an insulated frame wall cavity. The roof assembly is a traditional vented attic.
The interior gypsum board on the first floor should be considered “sacrificial” in that it cannot be readily cleaned, sanitized and dried after wetting. After a flood event wetted gypsum board should be cut away from wall assemblies above the wetting line. The use of non-water sensitive rigid insulation such as extruded polystyrene allows cleaning of rigid insulation surfaces. All wood framing surfaces on the interior of the CMU walls as well as interior wall framing should be coated/painted with acrylic latex paint prior to installation of interior gypsum board. The coating/ painting of all surfaces facilitates cleaning and sanitization after a flood event.
Figure 3 illustrates an alternative approach – the use of closed cell high density spray polyurethane foam (ccSPF) on the interior of the CMU walls and in the second floor frame wall cavity. Such foam has a low water absorption and is not damaged from flood waters. Again, all surfaces should be coated/painted with acrylic latex paint prior to installation of interior gypsum board – including the ccSPF.
--
Figure 3: Concrete Masonry Unit (CMU) Alternative Approach - Closed cell high density spray polyurethane foam (ccSPF) can be used on the interior of the CMU wall and in the second floor frame wall cavity. Such foam has a low water absorption and is not damaged from flood waters.
Figure 4 and Figure 5 are variations of CMU “raised slab foundations” but with frame wall assemblies rather than CMU assemblies. Both Figure 4 and Figure 5 have wall assemblies that are insulated externally with continuous exterior rigid insulation. They have no fibrous or batt insulation installed in frame wall cavities to further reduce risk of moisture damage arising from flood waters. Closed cell high density spray polyurethane foam (ccSPF) is installed in the frame wall cavities. Again, all surfaces should be coated/painted with acrylic latex paint including interior wall framing should be coated/painted with acrylic latex paint prior to installation of interior gypsum board.
Figure 4: Concrete Stem Wall Raised Slab Foundation – A variation of CMU “raised slab foundations” but with a frame wall. The frame wall assembly is insulated externally with continuous exterior rigid insulation. No fibrous or batt insulation is installed in frame wall cavities to further reduce risk of moisture damage arising from flood waters.
Figure 5: Empty Wall and Floor Cavities - Fibrous or batt insulation are not installed in wall cavities or floor framing cavities to further reduce risk of moisture damage arising from flood waters. The wall assembly is insulated externally with continuous exterior rigid insulation. Closed cell high density spray polyurethane foam (ccSPF) is installed in the frame wall cavities. Such foam has a low water absorption and is not damaged from flood waters.
Again, all surfaces should be coated/painted with acrylic latex paint including interior.
The spray foam should not completely fill the frame wall cavities thereby providing an air space that facilitates drying after a flood event. Again, note that wetted gypsum board should be considered “sacrificial” in that it cannot be readily cleaned, sanitized and dried after wetting. After a flood event wetted gypsum board should be cut away from wall assemblies above the wetting line. The air gap behind the remaining upper level of the gypsum board allows for air circulation and drying of the remaining surfaces.
Pier foundations must keep air and vapor out of the floor framing/floor assembly. Figure 6 and Figure 7 illustrate perimeter details – connecting the underside of the rigid insulation on the underside of the pier foundation floor framing through the perimeter rim joist area to the exterior wall assembly.
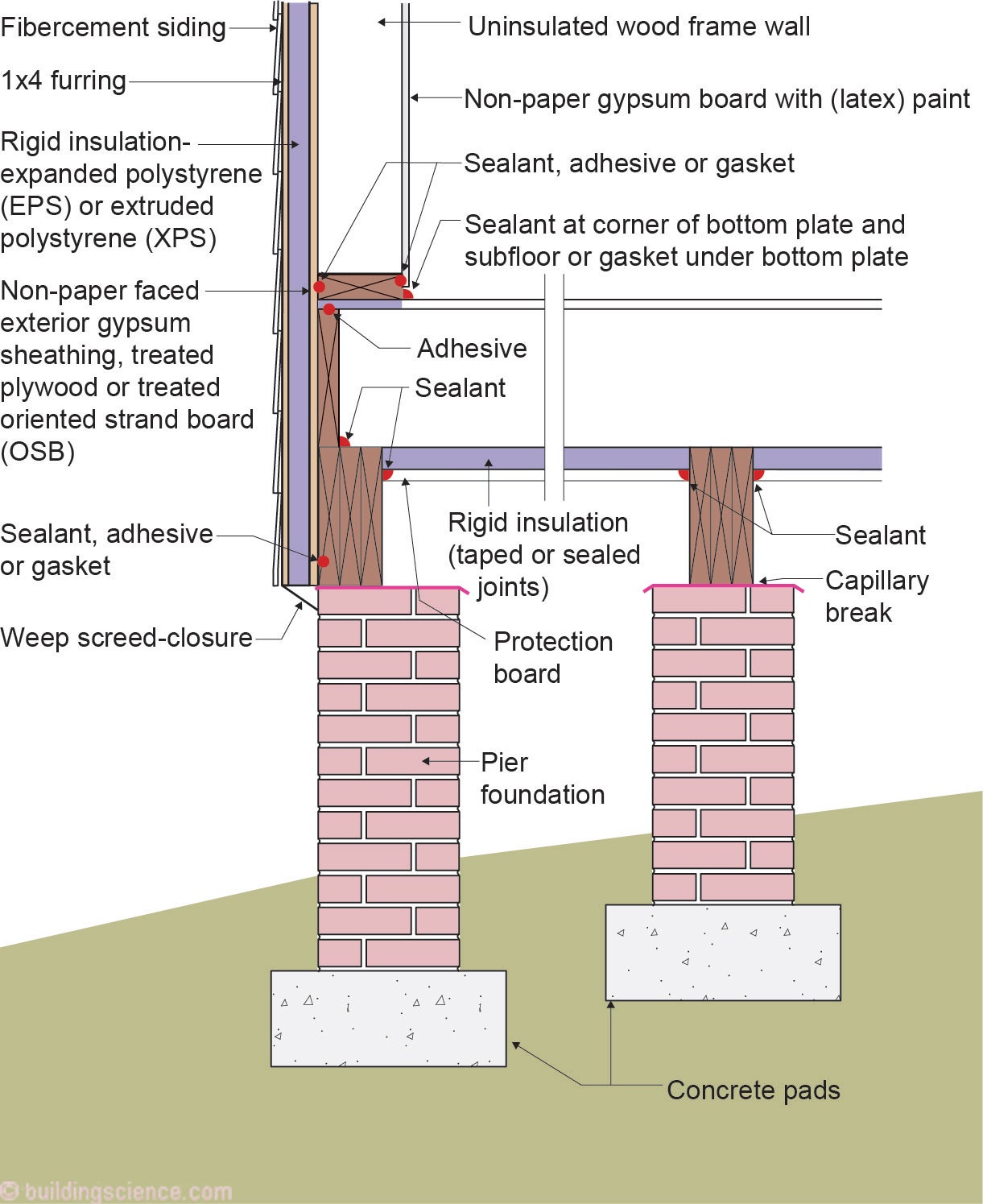
Figure 6: Empty Wall and Floor Cavities - Fibrous or batt insulation are not installed in wall cavities or floor framing cavities to further reduce risk of moisture damage arising from flood waters. The underside of the rigid insulation on the underside of the pier foundation floor framing must be connected through the perimeter rim joist area to the exterior wall assembly.
Figure 7: Pier Foundation - Pier foundations must keep air and vapor out of the floor framing/floor assembly. The underside of the rigid insulation on the underside of the pier foundation floor framing must be connected through the perimeter rim joist area to the exterior wall assembly.
Pest and insect control is provided by installing a protection board over the underside of the rigid insulation. Fiber Cement or cellular PVC boards work well in this regard. The fiber cement or cellular PVC boards should be installed using screws to allow for removal should flood waters rise above the floor framing level wetting cavities. The removal of the fiber cement or cellular PVC boards and rigid insulation and cavity insulation facilitates cleaning and decontamination of framing members. The rigid insulation should be considered “sacrificial” if wetted by flood waters.
No fibrous or batt insulation is installed in wall cavities or floor framing cavities to further reduce risk of moisture damage arising from flood waters. If closed cell high density spray foam is used in wall or floor framing cavities it still will need its exposed surfaces to be cleaned even though it is water resistant.
Figure 8 illustrates the use of an elevated concrete floor used in conjunction with concrete piers. Note that the concrete floor is insulated on the top surface to reduce thermal bridging as well as to further reduce risk of moisture damage arising from flood waters.
Figure 8: Elevated Concrete Floor - The concrete floor is used in conjunction with concrete piers. Note that the concrete floor is insulated on the top surface to reduce thermal bridging as well as to further reduce risk of moisture damage arising from flood waters.
Now onto the “problem child” foundation – crawl spaces. As mentioned many times previously (BSI-115: Crawlspaces - Either In or Out, March 2020)…there are two common crawl space foundation approaches - the crawlspace is either “vented” and “not conditioned” and connected to the “outside”…or…the crawlspace is “not vented” and “conditioned” and connected to the “inside”. Note that not vented conditioned crawl spaces are not considered occupiable or habitable space. It is not recommended to construct “not vented” and “conditioned” and connected to the “inside” crawl space foundations in flood prone and coastal regions.
Floors above crawl spaces should be constructed above the base flood elevation (BFE). The BFE should be at a minimum 12 inches below the lowest horizontal structural member.
Design and construct a crawl space that controls flood water by ensuring flood waters enter and exit the crawlspace without resulting in hydrostatic pressure differences. Water levels in the crawlspace should rise and fall at the same rate as the water level outside so that hydrostatic pressures are equalized (Figure 9). Sufficient openings need to be provided to control hydrostatic pressure. Water levels in the crawlspace should rise and fall at the same rate as the water level outside so that hydrostatic pressures are equalized. The total area (size) of all openings serving the crawl space should be equal to or greater than 1 square inch for every square foot of crawl space area. Note that vent openings typically contain a screen or a louver to control the entry of animals and these screens or louvers can block the flow of water. These openings should be distributed over the entire perimeter.
Figure 9: Controlling Hydrostatic Pressure – The crawlspace must control flood water by ensuring flood waters enter and exit the crawlspace without resulting in hydrostatic pressure differences.
Vented crawl spaces must keep air and vapor out of the crawlspace floor framing. Figure 10 illustrates the use of foil faced rigid insulation under the floor framing. The wood is warm and therefore dry – during both winter and summer. The foil facing on the rigid insulation addresses the vapor drive. The foil facing is an exceptional vapor barrier ( 0.1 perm). With the impermeable rigid insulation even relatively impermeable floor coverings such as vinyl flooring and polyurethane coated wood flooring work. The flow of vapor into the assembly (vapor drive) is less than the flow of vapor out of the assembly even with relatively impermeable floor coverings.
Figure 10: Cavity Insulation with Vapor Barrier - The foil facing on the rigid insulation addresses the vapor drive.
Adding fiberglass cavity insulation in conjunction with the impermeable foil faced insulating sheathing is a hybrid approach that uses the best qualities of both materials. Note that the optimum location for the airspace is above the cavity insulation. Makes for warmer floors – this is the same detail that should be used under bedrooms over garages.
Note that the rigid insulation also needs to be airtight. The seams should be sealed with foil tape. Figure 11 illustrates perimeter details. Again, pest and insect control is provided by installing a protection board over the underside of the rigid insulation.
Figure 11: Crawl Space Perimeter - Note that the rigid insulation also needs to be airtight. The seams should be sealed with foil tape.
Figure 12 illustrates an alternative approach – the use of closed cell high density spray polyurethane foam (ccSPF). Such foam has a low vapor transmission – less than 1.0 perm – and can be used with most floor finishes. If closed cell high density spray foam is used and gets wetted by flood waters it still will need its exposed surfaces to be cleaned even though it is water resistant. It is recommended that sill plates and rim joist framing be treated to be decay resistant.
Figure 12: Closed Cell Spray Polyurethane Foam - If closed cell high density spray foam is used and gets wetted by flood waters it still will need its exposed surfaces to be cleaned even though it is water resistant.
Where floods are concerned it is good to be “high and dry”…not a difficult situation and one where you are able to control the outcome.
Footnotes
___________________________________________________________________________________________________________________
1 The “Don’t get hit by a wave” saying comes from the folks at The Institute for Business and Home Safety (IBHS)…I sat through a bunch of their presentations in the early 2000’s and they warned us relentlessly about how powerful a wave is….I shamelessly have been using their saying ever since…IBHS inspired me to add the “Don’t get too wet” and “Make sure you dry” pieces…