The current building industry focus on durability is in part a reaction to the current perceived lack of it. Warranty claims and callbacks are increasingly leading to a rise in litigation and insurance costs. Another reason for the current focus on durability is the recognition that sustainability is not possible without durability. If you double the life of a building and you use the same amount of resources to construct it, the building is twice as resource efficient. It seems that one thing that both the development community and the environmental community can agree on is that durability is a good thing. What do we know about durability and how do we know it? The lessons of durability have come principally out of failure. Examining failures gives us guidance on increasing the durability of building constructions.
Durability Failures
In the last twenty-five years we can point to the following list of notable building industry failures:
Table 1: Notable Building Industry Failures 1980-2005
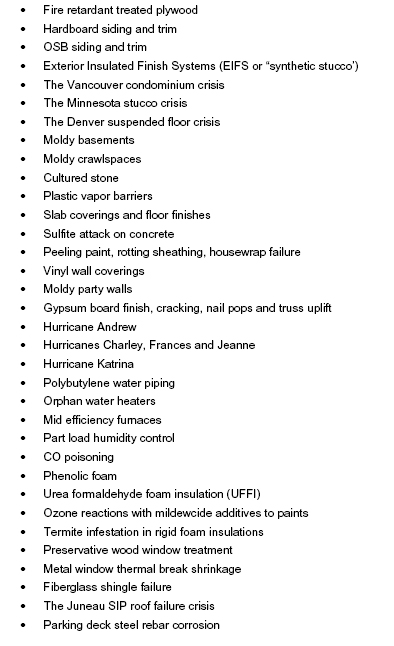
Taken collectively, these failures bracket our current understanding of building physics or building science. The failures define the limits of experience or the “state-of-the-art.”
What is telling from the list is that aside from Hurricane Andrew and Hurricane Katrina the issues are not structural in nature.
The structural wind loading lessons of Hurricane Andrew were incorporated into practice in less than a decade in Florida. When serious events happen serious actions follow. Failure drives change and leads to improvement. The hurricanes in Florida that followed: Hurricanes Charley, Frances and Jeanne resulted in water damage not structural damage to buildings constructed after the lessons of Hurricane Andrew were adopted into practice.
Unfortunately, the lessons of Hurricane Andrew were pointedly ignored in Mississippi, Alabama and Louisiana. It can be argued that the Hurricane Katrina damage (outside of the flooded areas of New Orleans due to levee breaches) is largely the result of stupidity rather than lack of knowledge. The structural provisions of the available model building codes were ignored or not enforced. In most jurisdictions where damage was extensive no building code of any kind was in effect. The FEMA guidelines for coastal construction were by and large ignored as well.
The Northbridge earthquake is not on the list as it is not considered a notable industry failure. However, the effects of the quake were examined, failures noted, and code changes followed. Again, failure drove change and lead to improvement.
It is argued here that durability issues are no longer structural in nature. It is difficult to recall the last major structural issue or notable structural failure in the building industry – residential or commercial. The only ones that come to mind, aside from Hurricanes Andrew and Katrina previously noted, are the Hyatt Kansas City walkway collapse, the Hartford Civic Center roof collapse, the Hancock Building glass failure and the Chicago Amoco Building marble failure. All occurred more than 25 years ago and all occurred in large commercial structures. And most structural engineers to this day deny that the latter two were structural issues arguing that they were building envelope cladding problems. The fact that glass and marble fell to the sidewalks in both cases appears to most civilians as being pretty structural is apparently lost on these structural engineers.
The building industry has collectively learned how to handle structural loads due to wind, hurricanes, earthquake, rain, ice, snow, gravity and soil movement. The exception is tornados and it is argued here that there is not much that can be done to protect against tornados that hit dead on – except providing hardened shelters – and providing warning. Like polio, humanity has cured durability issues related to structural engineering.
What is also telling from the list is that – aside from CO poisoning - the issues are water, heat, ultra-violet radiation and insect in nature. And of these issues water dominates by a wide margin. It is argued here that addressing water, heat, ultra-violet radiation and insects will significantly increase the durability of building constructions. This of course is obvious to most. What is not obvious is the connection of these factors to energy conservation.
Durability and Energy Conservation
Once constructed a building becomes a machine that “needs to be fed.” The more durable the building the longer it is around. The longer the building is around the more energy it consumes. Durable buildings need to be ultra energy efficient in order to be sustainable. Durability and energy efficiency are the cornerstones of sustainability.
One of the lessons of durability learned through failure is that as energy efficiency is increased durability is typically compromised. How can this be? One of the key elements of energy efficient building enclosures is a high level of thermal insulation. However, as thermal insulation levels are increased, the rate of building enclosure drying decreases. This affects building durability as it affects the moisture balance.
Another lesson of durability linked to energy conservation learned through failure is that insulating sheathings, a key element of energy efficient building enclosures are prone to insect infestation. Ground contact insulating sheathings can act as “insect interstates” that provide pathways into buildings. The failures associated with ground contact insulating sheathings lead to a building code prohibition for their use in regions with a high probability of termite damage.
Finally, one of the most poignant lessons of durability linked to energy conservation learned through failure is the one of CO poisoning. As the air tightness of building enclosures increases, the ability of combustion appliances to function is compromised. The durability issue here is the durability of the occupant. The failures associated with combustion appliances lead to building code changes and the development of new equipment and systems to address the failures.
The key role of water control in the durability of buildings has been long recognized and some good guidance on water control in buildings exists. Unfortunately, the guidelines on water control are not tuned or adapted to different uses and climates.
Additionally, what is missing is guidance on heat, ultra-violet radiation and insects. If the historical lessons of failure are matched with the appropriate physics and engineering judgment guidelines for the control of water, heat, ultra-violet radiation and insects can be developed for use in a practical durability standard and risk assessment protocol for use by designers, engineers, architects and contractors.
Limitations of Durability Standards or Risk Assessment Protocols
Failure mechanisms that happen for the first time typically cannot be prevented. It is unlikely that any durability protocol will be capable of preventing types of failures that have not already happened in the past.
Durability guidance is based on past experience – past failure to be specific. If buildings and assemblies are constructed consistent with current practice and past practice then the best that a durability standard or risk assessment protocol can hope accomplish is prevent known failure mechanisms. This in itself is a great benefit. However, this limitation must be understood.
Durability standards and guidance will not be able to prevent failures with new assemblies and new materials and new approaches – they will only be able to provide guidance to the developers and promulgators and innovators of new assemblies, materials and approaches on past experience and past mechanisms and with that guidance provide hope that any failures of new assemblies, materials and approaches are “new” in the sense that these failures could not have be prevented by knowledge of the “past.”
The best test of a durability protocol is how effective would it have been at preventing the known past failures. The list of industry failures at the beginning of this report should be the basis of evaluation of any new durability standard or risk assessment protocol.
Some of the failures previously listed would to this day be impossible to prevent with any practical durability standard or risk assessment protocol that is designed for use by designers, engineers, architects and contractors. For example problems with fire retardant treated plywood were a material science issue beyond the control of designers, engineers and contractors. Same for polybutylene water piping, mid efficiency furnaces, ozone reactions with mildewcide additives to paints, preservative wood window treatment, phenolic foam, urea formaldehyde foam insulation and fiberglass shingle failure. However, many of these, if not most, could have been prevented by sensible product design and testing.
The material science issues related to these failures need to be subject to an entirely different type of durability standard or risk assessment protocol. In other words, different durability standards and risk assessment protocols are necessary for designers, engineers, architects and contractors on the one hand and the developers and manufacturers of materials, components and equipment on the other hand.
The durability standard and risk assessment protocol discussed in this report is for the use of designers, engineers, architects and contractors designing and constructing buildings. The information in this durability standard and risk assessment protocol can be instructive to the developers and manufacturers of materials, components and equipment but by itself is entirely inadequate to the development of new materials, components and equipment.
Are there durability standards and risk assessment protocols currently available to the developers and manufacturers of materials, components and equipment that would have been able to prevent the problems associated with fire retardant treated plywood, polybutylene water piping, mid efficiency furnaces, ozone reactions with mildewcide additives to paints, preservative wood window treatment, phenolic foam, urea formaldehyde foam insulation and fiberglass shingle failure? Yes, but their limitation is also that of only being able to prevent “already known” failure mechanisms not new ones.
There is always inherent risk with innovation and progress and that risk will not be eliminated with durability standards or risk assessment protocols.
Damage Functions
The following is a list of the key damage functions affecting durability (presently known and understood):
Table 2: Damage Functions and Control Methods
From this listing of damage functions the first six are fire, structural and natural disaster in nature and are arguably addressed extremely well by the existing model building code (IRC) and FEMA. They will not be addressed further in this document beyond the following: “Follow the IRC building code and FEMA recommendations and your fire related, structural related or disaster related durability problems will not be completely eliminated but will be reduced to an acceptable level.” Acceptable level is of course open to discussion. A criteria of note is the recent experience with the three hurricanes that hit Orlando, FL in a 45 day period in August – September, 2004 (Hurricanes Charley, Frances and Jeanne). No one died, no roofs were lost, no facades were destroyed, no significant structural damage of any kind occurred to structures (homes in particular) constructed after the code changes implemented in 2001 (that are mirrored in the IRC). There was no call for building code changes from the insurance industry or from consumers regarding structural issues. The term “acceptable level” of problems appears appropriate.
The next 4 (water, heat, ultra-violet radiation and insects) are the main focus of this document and arguably address more than 90 percent of current industry durability issues.
Chlorides and sulphates are also arguably addressed extremely well by both the IRC and FEMA (Coastal Construction Manual). The risks associated with both of these damage functions are also dependent on water and therefore addressing the water damage function further reduces the risks associated with chlorides and sulphates. They will not be addressed further in this document beyond the following: “Follow the IRC building code and the FEMA recommendations (and the water damage function control methods) and you will not have chloride and sulphate related durability problems.”
Loading/abrasion/fatigue is also addressed in this document with the following limitations. This damage function is arguably a maintenance issue associated with “wear and tear.” It is also typically the purview of durability standards and risk assessment protocols for the developers and manufacturers of materials, components and equipment. It is not typically the purview of designers, engineers, architects and contractors except in the following context.
Many components will need to be replaced, serviced and maintained during the useful service life of the building. The ease of replacement, service and maintenance is within the purview of designers, engineers, architects and contractors. The building components that experience the greatest loading/abrasion/fatigue stress and that need regular replacement or maintenance or servicing are typically floor coverings – and their selection is within the purview of designers, engineers, architects and contractors.
The remaining damage functions (material incompatibility, oxides, ozone, oxidizing agents and solvents) are also not addressed. It is argued here that they are not significant enough issues to consider at this point in time for inclusion in a “practical” durability standard or risk assessment protocol for use by designers, engineers, architects and contractors. However, these damage functions are key to durability standards and risk assessment protocols for the developers and manufacturers of materials, components and equipment.
The four key non-structural or natural disaster damage functions of water, heat, ultra-violet radiation and insects will be discussed in terms of specific guidance and recommendations applicable to designers, engineers, architects and contractors. Additional discussion on the loading/abrasion/fatigue damage function within the context of replacement, servicing and maintenance will also be discussed.
Water
The water damage function and water control methods in buildings are based on the following factors:
the phases or states of water;
the water transport process or mechanism;
the driving forces or potentials for the transport mechanism;
the sources of water.
The phases (state), transport process or mechanisms and driving forces or potentials for water are listed below:
Table 3: Water – Transport Processes, Driving Forces and Potentials
The list in Table 3 is complete and captures the universe of phases and transport processes. Several of the processes are truly academic – thermal diffusion, Poiseuille flow and surface diffusion can be ignored and 99.9 percent of the mechanisms are captured.
The sources of water buildings must contend with are listed in order of priority based on historical experience as follows:
- rain;
- surface water;
- groundwater;
- occupants and occupant activities (interior moisture);
- atmosphere (exterior moisture);
- services (plumbing);
- building materials (construction moisture);
- snow and meltwater (ice damming).
The most historically successful methods of dealing with water have focused on the source approach whereby the major sources are sequentially and systematically addressed using an understanding of the phases, transport process and driving forces of water.
The largest sources of water are addressed first. For example rain and groundwater are addressed before occupant sources (interior moisture) and the atmosphere (exterior moisture). Continuing down the priority list occupant sources and the atmosphere are addressed before services and construction moisture. All are addressed, but resources are allocated based on the degree of risk and that is determined by source strength (geographic location or occupancy).
Table 4: Water Sources and Control Methods
This list of moisture sources and control methods should be the basis of a durability standard or risk assessment protocol that addresses the water damage function.
Since the water damage function is so significant in terms of durability that this list of moisture sources and control methods should not be “optional” and should therefore be considered a “pre-requisite” or “core element” or “requirement” for any durability standard or risk assessment protocol.
The list of moisture sources and control methods is based on ASTM E 241 – 04 “Standard Guide for Limiting Water-Induced Damage to Building.” When this list of moisture sources and control methods is coupled with the specific details contained in the EEBA Water Management Guide, the EEBA Builder’s Guides and the ASHRAE Journal Articles: “Understanding Vapor Barriers,” “Understanding Air Barriers,” “Understanding Drainage Planes,” “Moisture Control for Buildings” and “Residential Ventilation and Latent Loads” the water issue affecting the durability of building constructions can be addressed and hopefully, like polio, relegated to the margins of history.
Heat
The heat damage function and heat control methods in buildings are based on the following factors:
every 20 degree F reduction in the effective exposure temperature approximately doubles the useful service life of a material;
historical experience and exposure provide the basis for expected service life prediction.
The colder we make materials the longer they will last. Protecting critical elements from elevated temperatures can be done with thermal insulation, ventilation cooling and solar reflectance.
Arrhenius established the relationship of temperature on material durability over a century ago. The temperature relationship is very insightful: every 10 degree Kelvin rise in temperature decreases the service life of a material by half. It is important to note that the relationship is exponential.
A similar relationship exists with ultra-violet radiation. Over the intervening century the effects of temperature and ultra-violet radiation were also found to be synergistic and not just additive. The effects of temperature and ultra-violet radiation acting together are far more damaging that each acting independently of the other and then combining the damage.
Arrhenius pretty much made it clear that if you want things to last a long time keep them cool and don’t expose them to sunlight. Historical experience added water to the mix. If we add “keep it dry” to the list we have the marching orders for museums curators throughout the world: keep things dry, cool and don’t expose them to sunlight. Unfortunately for buildings we build them outside where things are not often dry, cool and protected from sunlight.
An approximation to the Arrhenius equation can be used for engineering purposes: every 20 degree Fahrenheit reduction in the average annual exposure temperature of a material doubles the useful service life of the material.
Consider the following strategy typically used by the building industry to deal with heat and ultra-violet radiation. Shingles and roofing membranes are the single most heat and ultra-violet radiation exposed elements. These materials often operate at temperatures exceeding 150 degrees F. We replace these elements typically on a 10-year to 20-year cycle based on exposure. The strategy is one of replacement – we don’t design them to last longer, we design them to be replaced and discarded.
Asphalt shingle roofs are lucky to last 10 years in Houston, TX but often last 20 years or longer in Minneapolis, MN. It is important to note here that the “warranty” offered by shingle manufacturers has nothing to do with service life prediction. The fact that the same warranty is offered for the same product regardless of where it is installed (i.e. Houston or Minneapolis) is telling. Even more telling is that color and orientation are also not considered. Geographic location, color and orientation are all key factors in determining effective exposure temperature and therefore are significant in service life prediction.
Now consider what happens if we locate a roofing membrane under thermal insulation and ballast rather than over the top of thermal insulation directly exposed to the elements? The membrane life becomes almost infinite as it now operates at room temperature throughout the life of the building and it is completely shielded from ultra-violet radiation. The stone ballast is the “sunscreen” or UV protection and the thermal insulation reduces the temperature stress over the critical membrane control layer. The strategy is referred to as the Inverted Roof Membrane Approach (IRMA) and is a practical application of the Arrhenius equation. Architects practicing “green” architecture who specify “green” roofs where plantings are located over roofing membranes accomplish the same thing.
Another approach is the use of surfaces that reflect solar radiation. White reflective roofs that reduce membrane roofing temperatures last longer – predictably longer – according to the Arrhenius equation.
However, radiant barriers that increase roof membrane temperatures and sheathing temperatures reduce durability – also predictably according to the Arrhenius equation.
The temperature of critical building enclosure elements can be used to assess the durability of those elements and the durability of the assembly.
The following is a list of building enclosure elements, expected service life and exposure. It is based on generic materials and past experience. Although the list is based on the heat damage function it includes the synergistic effects of ultra-violet radiation and water as these damage functions are not possible to separate or isolate in practice and are obviously part of the historical experience basis.
Table 5: Expected Service Life of Building Elements
Table 5 (continued): Expected Service Life of Building Elements
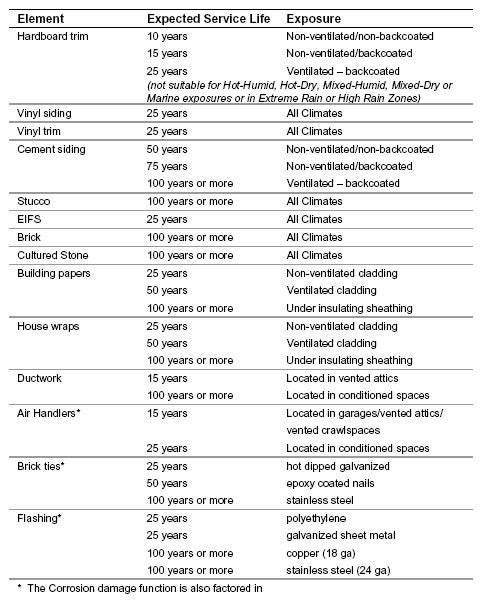
This list of building enclosure elements, expected service life and exposure should be the basis of a durability standard or risk assessment protocol that addresses the heat damage function (the synergistic effects of ultra-violet radiation damage function and the water damage function are included in this table).
A rating or points should be added or subtracted based on extending the expected service life of an element. Approaches that are not listed in the table can be evaluated using the Arrhenius engineering approximation or by accelerated lab testing (UV Arc, salt spray).
A baseline for each location can be established and should be the typical building constructed in a particular region. For example, consider a building constructed in Dallas, TX, which is a Mixed Humid Climate. The standard building is typically constructed with asphalt singles on the roof (10 year expected service life), vinyl siding on the walls (25 year expected service life) installed over a building paper (50 expected service life – vinyl siding is by definition a “ventilated” cladding).
If the vinyl siding is replaced with brick (100 year expected service life), the shingles replaced with slate (100 year expected service life) and the building paper covered with insulating sheathing (the building paper now has a 100 year expected service life) the building now can be considered “permanent” and therefore receive the highest durability rating or sustainability rating possible or have the lowest applicable risk.
Another example would be using a “cool roof shingle” in a Hot-Humid climate like Houston that reduces the temperature of the shingle by 20 degrees will increase the service life of the single by a factor of 2 from 10 years to 20 years. An obvious increase in rating or addition of points would be warranted in addition to the huge reduction in solar load and consequential increase in energy efficiency.
Points should be deducted and ratings reduced where longer life materials enclose or cover shorter life elements. For example, using a 100-year cladding system with 25-year ties over a 50-year housewrap should not be encouraged.
Ultra-Violet Radiation
The ultra-violet radiation damage function and ultra-violet radiation control in buildings is also based on Arrhenius. The effects of ultra-violet radiation on paints and coatings has been studied extensively and the dominant predictive service life models are Arrhenius based.
Surface treatments have been long known to be effective in protecting materials from damage from ultra-violet radiation. Paint on wood is an effective “suntan lotion” protecting the underlying wood from damage. Of course the paint coating itself experiences degradation from ultra-violet radiation. Paints are regularly formulated with UV absorbers and UV reflectors to enhance durability.
Where stable substrates are available (wood siding that is backventilated and otherwise not changing moisture contents widely and rapidly) most paint coatings on wood substrates are expected to last 10 years.
However, some types of paint coatings on architectural metals have a history of performance that can exceed 25 years.
Generally, the most resistant surfaces to ultra-violet radiation are unpainted surfaces such as stone, concrete, brick and unpainted stucco. Wood shakes that are “sacrificial” have also proven to be historically effective. Approximately 1/4 inch of wood is lost to ultra-violet radiation exposure every 25 years. The life of the wood shake is determined by the original thickness – the thicker the shake the longer it lasts.
Most sealant service lives are limited to 10 years due to ultra-violet radiation exposure.
The following is a list of building enclosure elements and expected service life is based on generic materials and past experience.
Table 6: Expected Service Life of Building Elements Exposed to Ultra-Violet Radiation
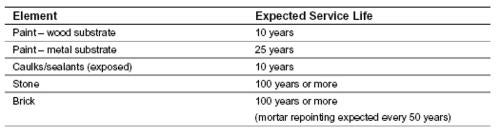
This list of building enclosure elements and expected service life should be the basis of a durability standard or risk assessment protocol that addresses the ultra-violet radiation damage function.
A rating or points should be added or subtracted based on extending the expected service life of an element.
Insects
Insects don’t behave according to Arrhenius. Food, water and habitat are the key elements for insects.
The key to insect control historically has been two pronged: chemical warfare and dealing with the food source: poison and kill them and don’t construct assemblies with materials that insects can eat or poison the materials so that the insects don’t eat them.
More recently has been the realization that denying the insects water and a habitat are also significant. For example, insects don’t eat foam based insulating sheathings but they sure do like living in them. Foam insulation is an excellent habitat if it is made accessible such as extending it into the ground.
Keeping materials dry also discourages insect infestation, but by itself that is not enough as insects can bring their own water with them (termite “tubes” provide a friendly micro-climate or habitat and a source of humidified air).
The insect damage function and insect control methods in buildings are based on the following factors:
- chemical treatment of soil;
- insect resistant building materials;
- control of habitat;
- control of water.
A degree of risk should be associated with location. In other words, the location establishes an “insect load” and the assembly or building should be designed and constructed the “resist the load”. The greater the “load” the greater the “load resistance” required.
The insect load should be based on historical experience such as Figure R301.2 (6) from the 2003 International Residential Code. The United States is broken down into four termite infestation probability zones: Very Heavy (I), Moderate to Heavy (II), Slight to Moderate (III) and None to Slight (IV).
Using the concept of infestation probability zones and a list of insect control methods a set of minimum requirements can be established per zone. For example, all of the methods would be required in the Very Heavy zone and most of the requirements would be waived in the None to Slight zone. In the other zones a mix of methods would be required.
The following list of control methods is based on these factors and the degree of risk or termite infestation probability.
Table 7: Insect Control Methods by Termite Zone
This list of insect control methods should be the basis of a durability standard or risk assessment protocol that addresses the insect damage function.
Loading / Abrasion / Fatigue
(Selection / Replacement / Maintenance and Servicing)
The loading/abrasion/fatigue damage function is considered in this document as a function of selection/replacement, maintenance and servicing. For example, the selection of a terrazzo floor rather than carpet impacts the issues of carpet replacement and cleaning.
Many components will need to be replaced, serviced and maintained during the useful service life of the building. As such the ease and cost of replacement, service and maintenance should be considered by designers, engineers, architects and contractors.
For example, sealed window glazing units have an expected (and historical) service life of approximately 25 years. These units will have to be replaced and maintained. Designs and constructions that improve the “ease” and cost of replacement and maintenance should be rewarded or encouraged. Windows themselves typically have a service life of 25 to 50 years and should also be designed to be replaced.
Similarly, locating an air handler in an attic with limited access knowing that the air handler has an expected (and historical) service life of approximately 15 years should be discouraged.
Floor covering service life is directly related to loading/abrasion/fatigue and clearly floor-covering selection is within the purview of designers, engineers, architects and contractors. With respect to floor coverings carpets should be assessed a 10-year useful service life and wood flooring and tile can be assessed a 100 year or greater useful service life depending on exposure. For example, wood flooring in the entrance lobby of an office building will not last 100 years, but can last 100 years in a bedroom. Porcelain tile is more resistant than ceramic tile and granite the most resistant of all.
The following is a list of building components subject to typical “wear and tear” replacement, maintenance and servicing issues and their expected service life:
Table 8: Expected Service Life of Heavy Use Building Components
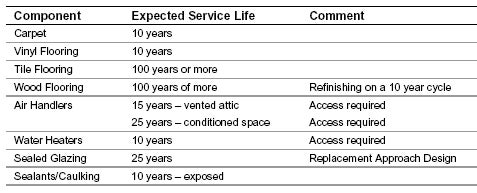
This list of building components and expected service life should be the basis of a durability standard or risk assessment protocol that addresses the loading/abrasion/fatigue damage function.
A rating or points should be added or subtracted based on extending the expected service life of an element such as a floor covering.
Points should be deducted and ratings reduced where provision for access for serving or replacement is not provided.
In terms of sealants or caulking, points should be added or ratings increased for designs that do not rely on sealants or caulking.
Proposed Durability Standard And Risk Assessment Protocol For Designers, Engineers, Architects and Contractors
The approach assumes that buildings are constructed to last 100 years or more. Individual elements or components are not assumed necessarily to last 100 years or more but are expected to be able to be serviced, maintained or easily replaced in order last 100 years or more.
It is further assumed that buildings are not considered durable by definition if the water damage function and insect damage function are not addressed.
However, “relative” durability assessments or “ratings” or “rankings” can be made by application of the heat, ultra-violet radiation, loading/abrasion/fatigue damage functions once the fundamental requirements of addressing the water damage function and insect damage function have been made.
It is also assumed that the service life of a material or component or assembly is not determined by the designer, engineer, architect or contractor, but has already been determined by historical experience in each region.
For example, selecting wood siding and installing the wood siding without back ventilation and backcoating will result in a service life of 25 years. This is a fixed value based on regional experience. However, ventilating and backcoating the same wood siding will result in a service life of 100 years or more. Again this is a fixed value based on regional experience.
In other words address the water damage function and the insect damage function as described in this durability standard and the building will be assumed to last 100 years or more. Individual elements or components will last as specified in this durability standard. Ranking or rating or relative comparisons can be made among the individual elements or components based on the service life established by historical experience in each region – also specified in this durability standard.
Finally, it is assumed that design and selection of elements, materials, components, equipment, systems and assemblies made by the designer, engineer, architect and contactor is executed correctly. This proposed durability standard does not address “quality control” but only addresses “quality assurance.” Quality assurance is the process of determining the design and quality control is the process of verifying that the design has been executed.
The framework for the proposed durability standard and risk assessment protocol is contained in Table 2. Guidance on water, heat, ultra-violet radiation and insects is added to existing guidance contained in the IRC and FEMA documents for wind, flood, earthquake, gravity and soil movement. Additional guidance on loading/abrasion/fatigue (“wear and tear”) is provided in the context of replacement, maintenance and servicing.
Step One: | Follow IRC and FEMA guidance |
Step Two: | Use Table 4 to address the water damage function |
Step Three: | Use Table 5 to address the heat damage function |
Step Four: | Use Table 6 to address the ultra-violet radiation damage function |
Step Five: | Use Table 7 to address the insect damage function |
Step Six: | Use Table 8 to address replacement/maintenance and servicing |
Specific numerical values for ranking purposes have not been assigned to the contents of Table 5, Table 6 and Table 8. The service life of the components is listed but the “value” of increasing or decreasing the service life has not been assessed nor has a “value” for service ease or cost been assessed. It is left to the individual user to determine these “values.”
Step One – Follow IRC and FEMA Guidance
This is self-explanatory. Design and construct the building to meet the applicable building code and FEMA guidelines.
Step Two – Use Table 4 To Address The Water Damage Function
The water damage function is addressed by targeting the sources of water. This is not an optional step. All sources of water need to be addressed. The following are mandatory requirements.
Rain
A drainage plane must be provided that is integrated with flashings. This is a requirement in all locations regardless of rain exposure. Another Building Science Digest contains a description of drainage planes (BSD-105: Understanding Drainage Planes).
A drainage plane must be accompanied by a drainage space. The EEBA Water Management Guide and the EEBA Builder’s Guides provide details to accomplish this.
Windows and doors must be “pan-flashed” in all but “low rain exposure regions” (less than 20 inches annual precipitation). The EEBA Water Management Guide provides details to accomplish this.
Reservoir claddings must be “uncoupled” from wall assemblies. Another Building Science Digest contains information to accomplish this (BSD-105: Understanding Drainage Planes).
Groundwater
A drainage plane must be provided with sub-grade drainage for below grade spaces. The EEBA Builder’s Guides provide details to accomplish this.
A capillary break separating the entire foundation from the soil must be provided. The EEBA Builder’s Guides provide details to accomplish this.
A vapor barrier separating the entire foundation from the soil must be provided. The EEBA Builder’s Guides provide details to accomplish this.
Occupants (Interior Moisture)
Ventilation (spot/source/dilution) according to ASHRAE Standard 62.2 must be provided.
Air Conditioning sized according to ACCA Manual J must be provided (except in IRC Zones 4- Marine or 6 or higher).
Part load dehumidification must be provided in IRC Zones 1 and 2 (“Hot-Humid Climates”) for buildings and units less than 2,000 square feet.
An air barrier must be provided. Another Building Science Digest contains a description of air barriers (BSD-104: Understanding Air Barriers).
Vapor control of wall, roof and foundation assemblies must be provided. Another Building Science Digest contains a description of vapor control measures (BSD-106: Understanding Vapor Barriers).
Atmosphere (Exterior Moisture)
Air Conditioning sized according to ACCA Manual J must be provided (except in IRC Zones 4- Marine or 6 or higher).
Part load dehumidification must be provided in IRC Zones 1 and 2 (“Hot-Humid Climates”) for buildings and units less than 2,000 square feet.
Ductwork must be airtight (less than 5 percent leakage).
Interior spaces must be air pressure balanced (less than 3 Pascals between all spaces).
An air barrier must be provided. Another Building Science Digest contains a description of air barriers (BSD-104: Understanding Air Barriers).
Vapor control of wall, roof and foundation assemblies must be provided. Another Building Science Digest contains a description of vapor control measures (BSD-106: Understanding Vapor Barriers).
Services
Plumbing should not be located in exterior walls.
Paper faced gypsum board should not be used in “wet areas.”
Washers should be equipped with single throw shut off valves.
Washers should not use rubber hose connections.
Wet rooms should have floor drainage.
Materials
Paper faced gypsum board should not be used in “wet areas.”
Paper faced gypsum board should not be used in multi-family party walls or any part of the building constructed before the roof is applied
Vapor open assemblies must be used. Another Building Science Digest contains a description of vapor control measures (BSD-106: Understanding Vapor Barriers).
Snow
Ductwork or air handlers must not be located in vented attics in IRC Zones 5 or higher.
An air barrier must be provided. Another Building Science Digest contains a description of air barriers (BSD-104: Understanding Air Barriers).
Step Three – Use Table 5 To Address The Heat Damage Function
The heat damage function is addressed by selecting the component and associated expected service life.
Step Four – Use Table 6 To Address The Ultra-Violet Radiation Damage Function
The ultra-violet radiation damage function is addressed by selecting the component and associated expected service life.
Step Five – Use Table 7 To Address The Insect Damage Function
The insect damage function is addressed by following the mandatory requirements in each insect infestation probability zone. This is not an optional step.
Step Six – Use Table 8 To Address Replacement/Maintenance and Servicing
Replacement, maintenance and servicing are addressed by selecting the component and associated expected service life.